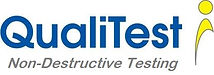
NDT Services
Use the left menu to navigate through the different services

![]() Suface CrackFound in welded hand rail during structure survey in USA | ![]() Surface CrackFound during new steel structure NDT for engineering office |
---|---|
![]() VT on petrol storage tankwith the aid of Rope Access | ![]() VT inspectionOn welded impeller |
![]() VT on welded rail jointShowing head defects | ![]() VT on a painted structureDuring adhesion Cross Cut technique |
Visual Inspection (VT)
Optical aids include low-power magnifiers, microscopes, telescopes and also specialised devices such as boroscopes, endoscopes and other fibre-optic devices for the inspection of restricted access areas. These devices can also be used with television camera systems. Much of the success of visual inspection depends on the surface condition and the lighting arrangements. Surface preparation such as cleaning and etching is often used and also surface replicas can be taken for both macro- and microscopic examination. In-situ metallography is also possible.
High-speed visual inspection with automated output is used for the inspection of the surface of sheet material and television techniques may use enhanced image and pattern recognition methods. Remote photography of inaccessible surfaces, such as inside a radioactive environment, is also possible. High-speed cine is also used for studying fast events. Arrays of optical diodes can be used instead of television cameras.
Typical inspections include:
-
Surface inspection of welding
-
Suface opening cracks
-
Surface corrosion pits etc.
-
Severe corrosion thining
-
Dimensional control
-
Assembly verification

Ultrasonic Inspection (UT)
Such mechanical waves can travel large distances in fine-grain metal, in the form of a divergent wave with progressive attenuation.The frequency is in the range 0.1 to 20 MHz and the wavelength in the range 1 to 10 mm. The velocity depends on the material and is in the range 1000-6000 m/s.
The technique detects internal, hidden discontinuities that may be deep below the surface. Transducers and coupling wedges are available to generate waves of several types, including longitudinal, shear and surface waves. Applications range from thickness measurements of thin steel plate to internal testing of large turbine rotors.
Most non-porous, resilient materials used for structural purposes (steel, aluminium, titanium, magnesium and ceramics) can be penetrated. Even large cross-sections can be tested successfully for minute discontinuities.
Ultrasonic testing techniques are widely accepted for quality control and materials testing in many industries, including electric power generation, production of steel, aluminium and titanium, in the fabrication of airframes, jet engine manufacture and ship building.
Ultrasonic Advanced Methods (TOFD, phased array etc)
There have been many developments and refinements to the fundamental ultrasonic technique to cater for improved performance and/or results. Read more...
Typical inspections include:
-
Surface inspection for surface opening cracks
-
Weld inspection - internal cracks , porosity , lack-of-fusion etc
-
Component inspection for internal fatigue cracks
-
Thickness measurements and corrosion surveys
-
Coating thickness measurements
-
Composite materials - detcetion of delamination and disbonds
-
Inspection of large series of bars and shafts.
![]() New Image 2 | ![]() SV103884 |
---|---|
![]() SV104517 | ![]() SV104772 |
![]() New Image 2 | ![]() DSCN0866 |
![]() Dscn0879 | ![]() DSCN0359 |
![]() DSCF0209 | ![]() DSCN3277 |
![]() DSC01010 | ![]() Test RA 12 |
![]() SV104772 | ![]() New Image 2 |
![]() DSCN3277 | ![]() DSCN3298.GGG |
![]() DSCN3275 | ![]() SV102526 |

Magnetic Particle Inspection (MT)
The specimen is magnetised either locally or overall, and if the material is sound the magnetic flux is predominantly inside the material. If, however, there is a surface-breaking flaw, the magnetic field is distorted, causing local magnetic flux leakage around the flaw. This leakage flux is displayed by covering the surface with very fine iron particles applied either dry or suspended in a liquid. The particles accumulate at the regions of flux leakage, producing a build-up which can be seen visually even when the crack opening is very narrow. Thus, a crack is indicated as a line of iron powder particles on the surface.
Fluorescent particles, which require UV-A illumination, are widely used and coloured particles are also available. The indications of cracks can be preserved by photography or by the use of peel-off transparent adhesive film. MPI methods can be applied to relatively rough and dirty surfaces, but the flaw sensitivity may be impaired.
The method is applicable to all metals which can be strongly magnetised – ferritic steels and irons, but not generally austenitic steels.
A 4,000Amp AC/HWDC fixed Installation is available for the inspection of components up to 2 meters in length.
Typical inspections include:
-
Surface cracks in steel welds and welded assemblies.
-
Engine components , crankshaft, gears, connecting rods etc.
-
Helicopter & Aircraft wheel bolts
-
Fuselage-wing attachments bracketry for YAK aircraft
-
Rapid inspection of large series of bars and shafts.
-
Heat Treatment cracks in components.
-
Fine surface defects in castings for use in high tolerance industries such as aerospace, automotive, oil & gas and medical components.
-
Fatigue cracks in components/fittings that have developed whilst 'in service
![]() SV105904 | ![]() SV105902 |
---|---|
![]() SV103900 | ![]() P1040771 |
![]() P1040910 | ![]() P1040754 |
![]() P1040765 | ![]() P1050205 |
![]() SV105204 Rotated AA | ![]() SV101226 |
![]() DSCN3343 | ![]() DSCN3347 |
![]() DSCN2240 | ![]() DSCN1033 |
![]() Copy of DSCN2230 | ![]() DSCF0008 |
![]() DSC01039 | ![]() MT Inspection on crank |
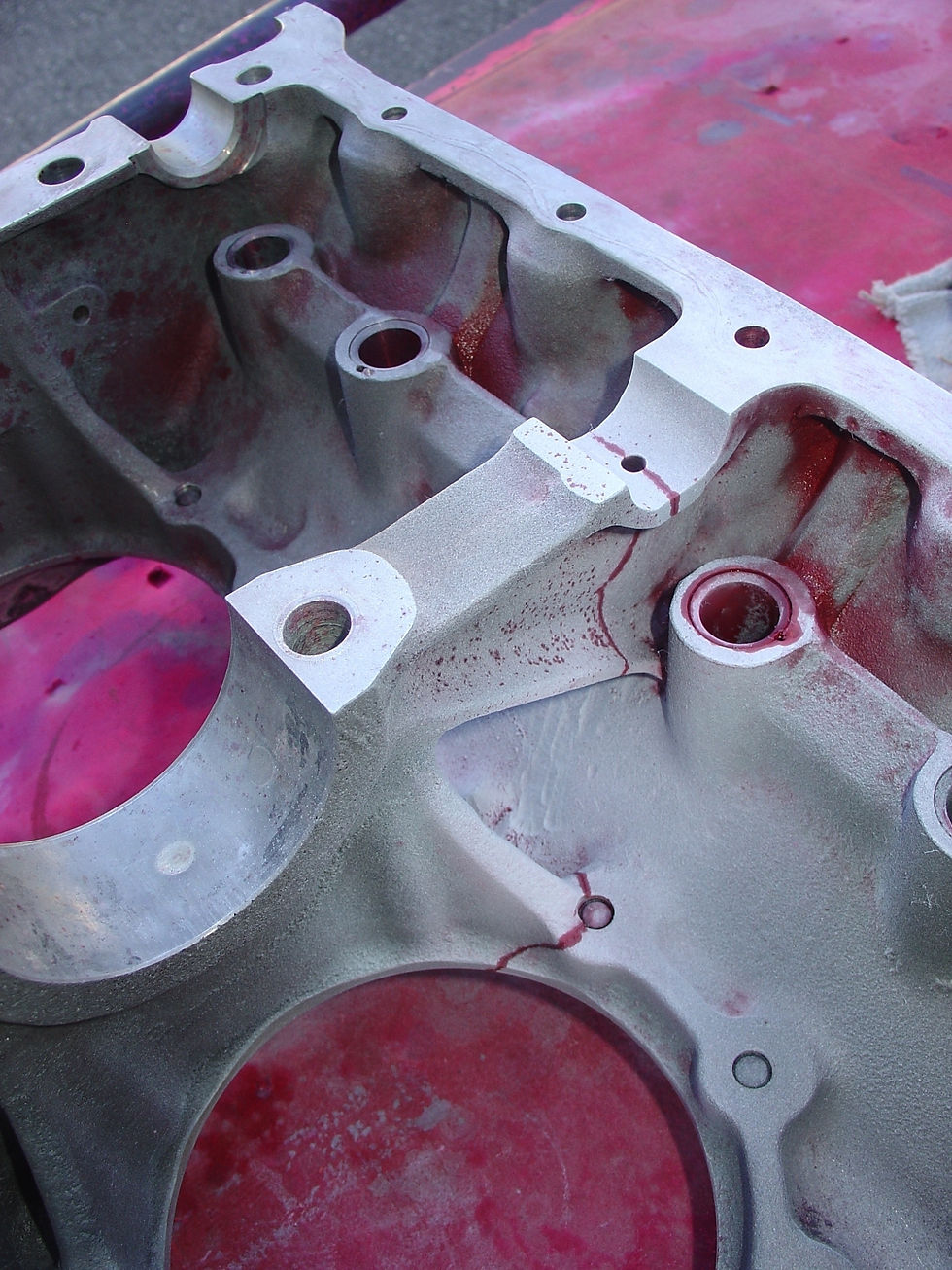
Liquid Penetrant Inspection (PT)
This is a simple low-cost method of detecting surface-breaking flaws such as cracks, laps, porosity, etc.
To be detected, the flaw must reach the surface to be tested.
Penetrant testing is one step up from visual inspection and offers many advantages, such as speed, large-area coverage and cheapness.
There are three major groups of penetrant process:
a) water-soluble
b) post-emulsifiable with water rinsing
c) solvent removable, the difference being in the method used to remove the excess penetrant.
In each of these three groups the penetrant solution can contain a dye to make the indication visible under white light, or a fluorescent material which fluoresces under suitable ultraviolet (UV-A) light.
Fluorescent penetrants are usually used when the maximum flaw sensitivity is required.
The principle of liquid penetrant testing is that the liquid penetrant is drawn into the surface-breaking crack by capillary action and excess surface penetrant is then removed; a developer (typically a dry powder) is then applied to the surface, to draw out the penetrant in the crack and produce a surface indication. Cracks as narrow as 150 nanometres can be detected. The indications produced are much broader than the actual flaw and are therefore more easily visible.
Liquid penetrant testing can be applied to any non-porous clean material, metallic or non-metallic, but is unsuitable for dirty or very rough surfaces. Surface cleaning is a vital part of the penetrant testing technique. The method can be manual, semi-automatic or fully automated. Penetrant inspection, continuous-operation production lines in which the specimens are cleaned, dipped, washed, dried, etc on a time cycle are common.
Recently, equipment to fully automate the visual inspection stage of the process, by robotic handling of the specimen on a programmed procedure with television camera viewing and pattern recognition to identify and recognise flaws, has been introduced. Television image enhancement processes can be included.
A special, very high sensitivity penetrant process, using radioactive tracers is sometimes used, but requires very stringent safety procedures.
Typical inspections include:
-
Suface opening cracks
-
Surface corrosion pits etc.
-
Aerospace components and structures
-
Medical devices
-
Aluminium components
-
Titanium components
-
Fasteners
-
Fatigue cracks in components/fittings that have developed whilst 'in service
![]() Flourescent Penetrant InspectionPeriodic inspection on wing attachment bolt holes | ![]() Flourescent Penetrant InspectionPeriodic inspection on wing attachment bolt holes |
---|---|
![]() Flourescent Penetrant InspectionCrack found during overhaul inspection on a 4 Cylinder Aero engine aluminium crankcase | ![]() Flourescent Penetrant InspectionCrack found during overhaul inspection on a 4 Cylinder Aero engine aluminium crankcase |
![]() Flourescent Penetrant InspectionCrack found during overhaul inspection on a 4 Cylinder Aero engine aluminium crankcase | ![]() Flourescent Penetrant InspectionCrack found during overhaul inspection on a 4 Cylinder Aero engine aluminium crankcase |
![]() Flourescent Penetrant InspectionCrack found during overhaul inspection on a 4 Cylinder Aero engine aluminium crankcase | ![]() Flourescent Penetrant InspectionCrack found during overhaul inspection on a 4 Cylinder Aero engine aluminium crankcase |
![]() Flourescent Penetrant InspectionTIG & Laser weld inspection on medical device - stainless steel | ![]() Red Dye Penetrant InspectionUsing Rope Access on a MIT installation in the USA |
![]() Flourescent Penetrant InspectionLine Penetrant system installed at our Collombey site , offering Type 1 (Fluorescent) , Sensitivity Level 2 & 3 inspection in accordance with ASTM-1417 | ![]() Flourescent Penetrant InspectionPeriodic Inspection on wing attachment bolt holes |
![]() Red Dye Penetrant InspectionDuring evaluation and training exercise | ![]() Flourescent Penetrant InspectionPeriodic inspection on wing attachment bolt holes |
![]() Red Dye Penetrant InspectionCrack found during overhaul inspection on a 4 Cylinder high performance race car engine crankcase | ![]() Flouresent Penetrant InspectionSatellite mirror panel , using high sensitivity water washable / Level 3 |
![]() Flourescent Penetrant InspectionCrack found during overhaul inspection on a 6 Cylinder Aero engine aluminium crankcase | ![]() Flourescent Penetrant InspectionTIG & Laser weld evaluation on medical device - showing porosity |
![]() Flourescent Penetrant InspectionTIG & Laser weld evaluation on medical device test parts | ![]() Flourescent Penetrant InspectionTIG & Laser weld inspection on medical device - stainless steel |
![]() Flourescent Penetrant InspectionTIG & Laser weld evaluation on medical device test parts |
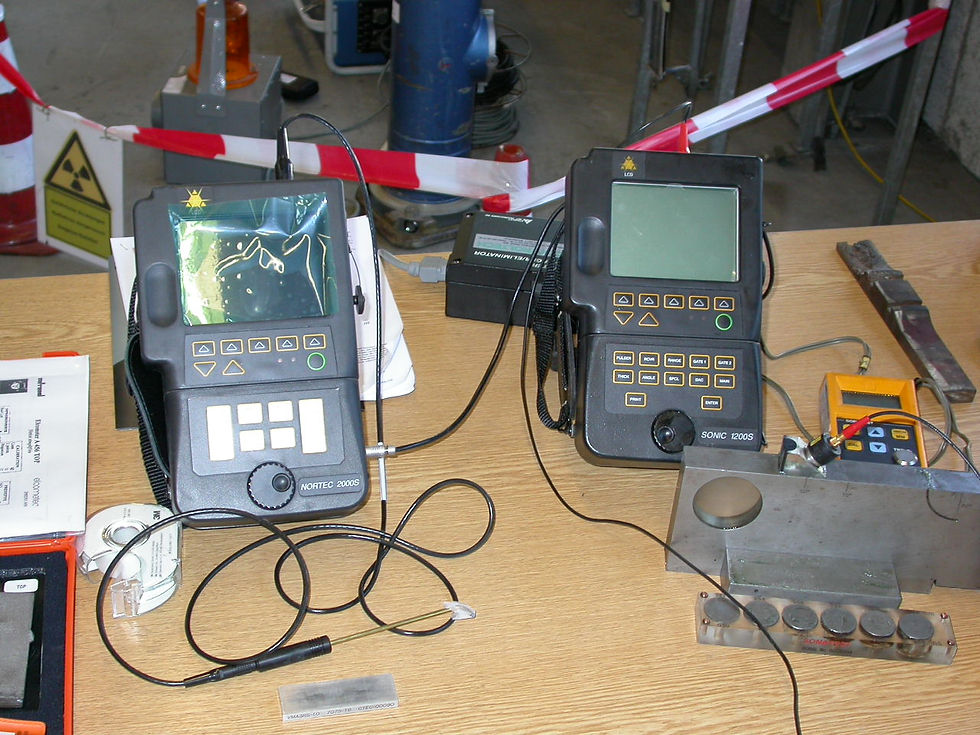
Flaws and material variations in the specimen affect the strength of the eddy currents.
The presence of flaws etc is therefore measured by electrical changes in the exciting coil. Both voltage and phase changes can be measured, but some simpler instruments measure only the voltage changes.
The strength of the eddy currents produced depends on the:
a) electrical conductivity of the specimen;
b) magnetic permeability (for a ferromagnetic specimen);
c) stand-off distance between the specimen and coil;
d) AC frequency used in the exciting coil;
e) dimensions of the coil and specimen;
as well as the presence of flaws, and much of the success of eddy current testing depends on separating the effects of these variables. Most eddy current instruments require calibration on a set of test specimens and the flaw sensitivity can be very high.
Equipments vary from simple portable meter read-out instruments to more complex oscilloscope read-out displaying both phase and voltage; recently the outputs have been digitised to produce fully-automated computer-programmed equipment with monitored outputs for high-speed testing.
Applications vary from crack detection, to the rapid sorting of small components for either flaws, size variations or material variation. Many applications are to bar, tube and wire testing. Metal sorting is also a common application of eddy current testing
Typical inspections include:
-
Surface Inspection - Surface cracks in machined parts and metal stock
-
Inspection of the area around fasteners in aircraft and other critical applications
-
Corrosion Detection - detect and quantify corrosion on the inside of thin metal such as aluminum aircraft skin.
-
Bolt Hole Inspection - Cracking inside bolt holes can be detected using bolt hole probes
-
Tubing inspection - Both in-line inspection of tubing at the manufacturing stage and field inspection of tubing like heat exchangers are common eddy current applications. Both cracking and thickness variations can be detected
-
Conductivity Testing - to identify and sort ferrous and nonferrous alloys, and to verify heat treatment.
![]() | ![]() |
---|---|
![]() | ![]() |
![]() | ![]() |
![]() | ![]() |
![]() |

Radiographic Inspection (RT)
Radiography uses X-rays or gamma-rays to produce an image of an object on film. The image is usually natural-size. X-rays and gamma-rays are very short wavelength electromagnetic radiation which can pass through solid material, being partly absorbed during transmission. Thus, if an X-ray source is placed on one side of a specimen and a photographic film on the other side, an image is obtained on the film of the thickness variations in the specimen, whether these are surface or internal.
This is a well-established technique which gives a permanent record and is widely used to detect internal flaws in weldments and castings and to check for mis-constructions in assemblies.
The source of radiation is either an X-ray tube or a pellet of radioactive material emitting gamma-radiation. X-ray equipment is usually described by the electrical voltage across the X-ray tube: thus, 300 kV X-rays. The higher the voltage, the greater the penetrating power of the radiation; industrial X-ray equipment ranges from about 20 kV to 20 MV and the most powerful equipments can be used to radiograph up to 500 mm (20") steel.
Nearly all gamma-radiography is done with either cobalt-60 or iridium-192 sources; there are a few other radioactive isotopes suitable for gamma-radiography, for special applications.
To obtain images with good definition it is desirable to have small-diameter radiation sources and the effective source size of typical X-ray and gamma-ray sources is in the range 1 to 4 mm diameter. After the radiographic film has been exposed, it has to be photographically processed (develop, wash, fix, dry) and is then placed on an illuminated screen for visual interpretation of the image. X-rays and gamma-rays are dangerous and radiographic equipment must be used either inside a protective enclosure, or with appropriate barriers and warning signals, to ensure that there is no radiation hazard to personnel. Qualified staff must be employed.
Radiography on film is a relatively expensive NDT method, due to the cost of the film. The larger X-ray equipments (for thick specimens) are also costly and require costly protective enclosures. Gamma-ray sources are much less expensive and are widely used on site work because of their greater portability. Generally, exposure times in gamma radiography are much longer than with X-rays.
The type of source used, and the image recording system, radiographic film, image intensifiers, cine film, video recording, will depend on the type of event that is required to be studied, and the thickness and density of the subject.
X-ray sources may be constant potential, (half-wave generators are of limited use); repetitively pulsed eg linear accelerators; or single pulse eg flash pulsers. Gamma-ray sources may be used where long-term movement caused by changes in stress or temperature are required to be measured.
Fast moving images may be recorded at very high frame rates using suitable cine cameras or high-speed video systems allowing slow-motion replay, or ‘frozen’ on X-ray film using flash pulser X-ray sources with pulse durations of 20 to 50 nanoseconds, when suitable synchronising systems are used.
Repetitively pulsed sources may be synchronised to cyclic rotational events, yielding techniques of strobo-radiography/radioscopy. Variable precession of the synch pulses enables examination of whirl and vibration amplitudes of rotating shafts or assemblies from differing angles, and slight variations in the frequency of the X-ray pulses can yield slow-motion presentations of high-speed events.
Typical inspections include:
-
Surface inspection of ferritic steels
-
Engine components , crankshaft, gears connecting rods etc.
-
Helicopter & Aircraft wheel bolts
-
Fuselage-wing attachments bracketry for YAK aircraft
-
Weld inspection
-
Rapid inspection of large series of bars and shafts.
![]() DSCF0002 | ![]() front page |
---|